The automotive industry is continually evolving, pushing companies to seek innovative solutions that boost efficiency and sustainability. As a vital link in the supply chain, packaging plays a critical role in this process. Expanded Polypropylene (EPP) has emerged as a game-changing material in automotive packaging, offering a range of benefits that address the industry’s core challenges. This article will explore the properties of EPP and its applications in automotive packaging, along with the benefits it offers manufacturers and environmental considerations to keep in mind.
What Is Expanded Polypropylene (EPP)?
Expanded Polypropylene (EPP) is a lightweight foam material produced by expanding polypropylene resin into resilient beads. These beads are molded into various shapes and densities to meet diverse packaging needs. The material’s closed-cell structure naturally enables shock absorption, offering excellent performance under repetitive stresses. Moreover, EPP is designed to be fully recyclable, making it particularly attractive for companies seeking to lower their environmental footprint without sacrificing quality.
EPP Solutions in Automotive Packaging
Automotive supply chains face challenges such as protecting fragile parts, reducing shipping expenses, and adhering to strict environmental standards. EPP addresses these issues by providing a material that is not only durable but also sustainable. Many companies also integrate EPP solutions with other packaging options, such as corrugated plastic containers, to create a robust, multi-layer protection system that simplifies handling.
Key Benefits of EPP for Automotive Packaging
EPP is a material that offers a range of benefits, making it an attractive option for automotive packaging:
- Lightweight Efficiency: With an impressive strength-to-weight ratio, EPP reduces overall packaging weight. This lightweight efficiency translates into lower shipping costs, reduced fuel consumption, and diminished carbon emissions.
- Superior Impact Protection: Its shock-absorbing properties ensure that delicate and high-value components are protected during transit, minimizing losses and reducing replacement costs.
- Customizable Fit: EPP can be precisely molded to the contours of automotive parts, achieving a secure enclosure that minimizes movement during shipping. This is especially valuable when employing custom-molded containers for unique component geometries.
- Cost-Effective Lifecycle: Although initial costs in implementing EPP may be higher, its reusability and long lifespan yield long-term savings by reducing reliance on disposable alternatives.
- Environmental Sustainability: As a material that is 100% recyclable, EPP supports a shift towards a circular economy while promoting overall environmental sustainability.
Applications of EPP in Automotive Packaging
EPP’s versatility makes it an ideal material for a range of automotive applications. Its properties allow it to serve multiple functions in packaging and transport:
- Custom-Molded Containers: EPP can be engineered into containers or trays that perfectly conform to the shape of critical automotive parts—such as sensors, dashboards, and bumpers—ensuring adequate protection during transit. These custom-molded containers optimize fit and security.
- Dunnage for Secure Transit: By forming structured compartments, EPP dunnage prevents parts from colliding and helps maintain organized loading and unloading procedures.
- Reusable Packaging Systems: Thanks to its durability, EPP facilitates the development of returnable packaging solutions. Reusable systems minimize waste and lower both material and disposal costs over time. Additionally, EPP can be combined with foam assemblies to protect especially delicate components that require layered cushioning.
- Efficiency on the Assembly Line: Custom-designed solutions, such as specialized EPP trays and bins, streamline assembly operations by organizing smaller components for quick access, thus accelerating production processes.
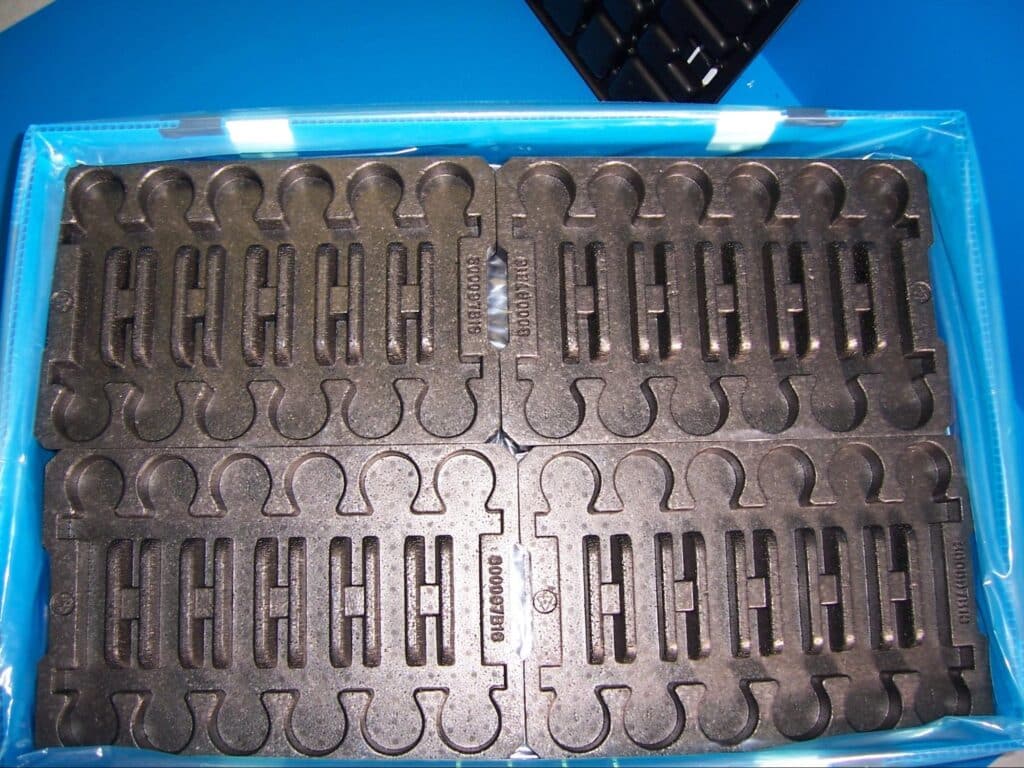
EPP’s Role in Enhancing Transport Efficiency
Efficient transportation is critical in automotive logistics, and EPP plays a key part in achieving this goal:
- Cost Savings Through Lighter Loads: The reduced weight of EPP packaging results in lower fuel consumption and shipping expenses. This directly impacts overall logistics costs and supports environmentally friendly practices.
- Optimized Cargo Space: The ability to tailor packaging shapes allows for maximized use of available space. By achieving more efficient loading, companies can reduce the number of trips needed for transport.
- Streamlined Handling: Precision-molded containers not only secure components but also simplify loading procedures, contributing to overall smoother logistics operations.
- Minimized Damage and Downtime: By reducing the possibility of shipping damage, EPP helps ensure that components reach manufacturers in pristine condition, thereby minimizing production delays.
Environmental Advantages of EPP
Sustainability is a key driver in modern automotive packaging. EPP offers clear environmental benefits without compromising performance:
- Reusability and Recyclability: EPP packaging can be used multiple times before recycling is required, lessening the demand for raw materials and reducing waste.
- Support for a Circular Economy: By relying on materials that can be reused and recycled, EPP helps automotive companies transition toward circular practices and longer product lifecycles.
- Eco-Friendly Production: The production of EPP requires less energy and fewer chemicals compared to other materials commonly used in packaging. This supports the automotive industry’s efforts to reduce its environmental impact.
Challenges and Practical Considerations
Transitioning to EPP packaging may present initial challenges such as higher upfront costs and logistical adjustments. However, the long-term benefits—cost savings from reduced transportation expenses, extended packaging lifecycle, and enhanced sustainability—often outweigh these concerns. With proper planning and strategic coordination across production facilities and distribution channels, companies can overcome these transitional hurdles. Additionally, clean and repair services can extend the lifecycle of EPP packaging, ensuring it remains effective through multiple shipping cycles. By implementing these steps, organizations will maximize EPP’s value and minimize disruptions to their existing workflows.
Universal Package’s EPP Solutions for Automotive Packaging
Universal Package specializes in custom EPP packaging solutions tailored to the specific needs of automotive manufacturers. The company combines technical expertise with a collaborative approach, offering everything from custom-molded containers to fully integrated returnable systems. By advising on logistics integration and providing tailor-made designs, Universal Package helps automotive businesses streamline operations, protect sensitive parts, and meet sustainability targets.
Why EPP is Paving the Future of Automotive Packaging
Expanded Polypropylene (EPP) is redefining automotive packaging with its lightweight, impact-resistant, and sustainable properties. It meets the dual demands of protecting valuable components and reducing shipping costs while supporting environmental responsibility. As the automotive industry continues to prioritize efficiency and eco-friendly practices, EPP stands out as an innovative solution driving modern packaging forward.
Ready to optimize your automotive packaging? Partner with Universal Package for custom EPP solutions that safeguard your components, lower operational costs, and advance your sustainability initiatives.